The Limitations of PLM Software
All manufacturing organizations rely on some level of product lifecycle management (PLM)–whether through dedicated software or in-house solutions–for successful product creation. As discussed in my previous blog, PLM software provides accessibility and product consistency to engineering teams, but the advantages and benefits tend to be constrained to those teams. Before organizations can fully take advantage of the PLM approach’s benefits, they must realize the limitations of today’s PLM software solutions.
Changing an enterprise-wide PLM system is like changing the course of an aircraft carrier.
Inability to adapt quickly limits PLM software capabilities
Fully embracing PLM proves to be a challenge for both product organizations and technology providers. It’s no surprise how rapidly technology evolves. PLM software companies can integrate some changes with relative speed. However, companies using the technology are slow to adopt the changes. No matter the reason – such as expense or time – changing an enterprise-wide PLM system is like changing the course of an aircraft carrier.
Primary PLM software providers attempt to manage the constant barrage of technology changes by integrating modules into their software solution. Unfortunately, the new modules aren’t integrated well with the core PLM software due to rapid acquisition in the late 1990s and early 2000s. Organizations may offer the new technology, but the appropriate teams can’t leverage the modules efficiently. As a result, teams choose not to – or simply can’t – adopt the modules.
6 Limitations of a PLM software-driven perspective
This example of modularity is only one way that PLM software providers aren’t fully realizing the limitations on their solution. Despite the desire to create a seamless tool, PLM solutions are proving to be a roadblock to product design, alignment with manufacturing, and an enterprise-wide product lifecycle.
1. Rigid PLM systems lead to wasted time or costly workarounds
PLM software solutions are rigid structures. In contrast, engineering teams need a flexible and adaptable solution to work efficiently. This triggers a cause-and-effect where the product teams believe that the PLM systems hinder progress, so they often find workarounds that have negative consequences. Users will frequently work outside the system to speed up the product development process. For example, a user may email CAD models to suppliers without alerting the product owners or managers. As soon as this happens, the product loses consistency, version control, and IP protection.
There is no one-size-fits-all solution when it comes to PLM software or processes.
2. A software perspectives hinders problem-solving
The data entered into the PLM software must be high quality in order to have valuable information returned. And, decision-makers must use the data efficiently. In dynamic team environments, people in dispersed locations (often in different organizations) must work together to make decisions quickly. When design problems arise, it’s easy to blame the PLM software, but that is a narrow view. Teams must evaluate the PLM software, engineering methods, and data quality to determine the true root cause.
3. Required customization wastes company resources
There is no one-size-fits-all solution when it comes to PLM software or processes. Companies typically want to configure and customize the PLM software to their own needs. When it comes to usability, organizations tend to use the configuration tools supplied by the software vendor. However, deeper customization requires writing new code which may need to be outsourced. This process is extremely labor-intensive. Worse, whenever an updated platform releases, the customized elements are at risk of breaking, requiring special regression testing.
4. Incompatible files require exceptional admin work
Organizations in the manufacturing industry frequently create and manage information in their own formats, such as:
- Native CAD formats
- Neutral file formats
- Lightweight visualization formats
Users need to share this information throughout an organization or with external partners, but the formats are rarely compatible. When this happens, the users have to go through a time-consuming process to convert the file. The conversion can often result in data loss, such as geometry features, notations, and metadata. Furthermore, the conversion requires extra work on the user, disrupting and distracting from pressing product deliverables. Instead of spending time to translate the file, users may attempt a shortcut by grabbing a screen capture or finding another means of sharing content.
5. Legacy systems and data don't integrate well in enterprise PLM systems
The old adage about teaching old dogs new tricks can be overcome, but expect it to be a long process. When a company has been relying on a particular process for a long time, there are vast libraries of data that must be migrated to a new system. These legacy methodologies, systems, and data prove difficult to integrate. In an enterprise PLM system, organizations need to:
- Integrate old data with other data types
- Align legacy data to the PLM data model
- Cleanse the data and standardize the information
- Train users where to find newly migrated data
- Understand and manage the impacts of integrating the new tool
6. Resistant company culture requires education and training
Perhaps the biggest issue is the sheer enormity of resources required for deploying a complex PLM system. Much of the hesitation to PLM lies in a company’s culture. This can only be changed by educating companies to the value of PLM as an approach, and by providing training to users once the software has been rolled out. In addition to training, organizations need to ensure that the right supplemental tools are in place for optimal workflows. My friend and colleague Don Haupt, the retired technical steward of PLM and engineering systems at Caterpillar, has this to say about implementing PLM:
“Adopting PLM as a business strategy, and making the necessary process changes and technology implementations is not a trivial matter. It takes a significant investment in both time and money, even if you’re starting with a mostly ‘clean sheet of paper.’ The return on the investment can be substantial, but the short-term focus and immediate returns expected in today’s business climate often stop a PLM implementation before it even gets started.”
STEPPING BEYOND PLM SOFTWARE
The momentum created by Industry 4.0 exposes that the industry’s expectations for PLM are misleading. Although the industry hoped for a tool that would streamline the process and resolve problems, PLM software alone simply can’t fix it. Not all hope is lost – this opens up a unique opportunity for organizations to examine other symbiotic solutions in their product development philosophy that lie beyond the realm of PLM software.
Much of the hesitation to PLM lies in a company’s culture.
The last three blogs provide understanding of the current atmosphere surrounding PLM as a software and a business approach. This will provide a strong foundation in discussing the future of Industry 4.0. In the next blog, I addressed what the future of smart manufacturing will look like once companies embrace a PLM approach rather than viewing it as a singular software solution.
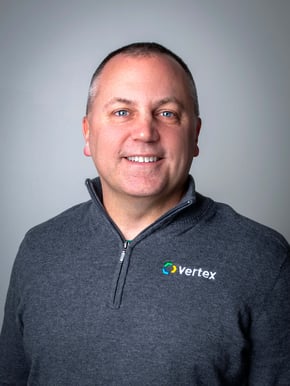
COMMENTS