The Future of Manufacturing: True Alignment Between Silos
Aggregating data across silos into an accessible digital twin creates a lot of opportunities for improvements within manufacturing. I think a key change we will see in the coming months is to develop true feedback loops. Right now, information can only move in what I call a “left to right” flow from engineering down through procurement, manufacturing, marketing, sales, and service. As it passes from one silo to the next, each department has to consume different pieces of information that they need to make decisions, harvest new pieces of information, and then push it onto the next team.
I suspect all readers will agree that this downstream information flow is extremely challenging. But it’s nearly impossible to flow “right to left”. This has always been a challenge. As digital transformation accelerates, there’s opportunity to create true alignment between the different silos as they consume and interact with a digital twin.
The Service Team Conundrum
The concept of the digital twin within engineering departments has been around for decades. Only in recent years has the phrase made it into the “mainstream” of an enterprise. A digital twin implies that everyone in an extended enterprise has access to a digital representation of the product they’re working on. This gives them a basis to communicate and connect everyone together.
The trick with the digital twin is making sure it’s easily accessible by anyone in your organization. Take for example your service team. Service departments typically draw the shortest straw when it comes to the tools and technology to access product data and visuals. This is partially because of the heavy capital cost of hardware and software technology, and the training to go with it. Also consider the high cost of a service technician’s time. These individuals have to get their service tasks done in a very short amount of time and with quality so they can move on to the next job.
A digital twin promises to give service technicians the ability to immediately understand the product, fill out a service report using visuals, and provide serviceability improvement. For example, using Vertex enables a service technician to quickly visualize their current job and get accurate, up-to-date work instructions on the spot. They can access instructions on a mobile device with full fidelity. Additional value with this allows technicians to immediately pull up the part that broke and add a comment regarding the issue. This information can seamlessly push “right to left” to engineering and manufacturing teams to identify recurring problems, areas for optimization, and opportunities to align silos in a way never done before.
The key here is not only how rapidly a service technician views their data in the context they need but also how the information is delivered. The team doesn’t need to utilize an engineering tool that can be cumbersome to use or have a high learning curve. Companies use Vertex to communicate along the digital thread with a low cost, easily accessible solution to align data for contextual viewing.
The Digital Twin on the Manufacturing Line
Let’s look at another example of how digital twins align silos to optimize operations on the manufacturing line. In addition to providing work instructions for the manufacturing line, they can also provide feedback “right to left.”
For example, it can be common to assemble something incorrectly because the shape of a part is easily misoriented. Vertex lets workers capture the concern, which funnels back to the engineering team who can then improve the design. Even something as simple as turning a component from a square shape into a rhombus shape can make a big difference on the factory floor, even if it doesn’t greatly impact the part performance or cost.
Management or data quality teams can review dashboards with Vertex-enriched visuals, allowing them to visualize areas of concern. Once manufacturing, production, and service can communicate challenges between the silos, they can make better decisions for all groups across the enterprise. That stands to save companies countless dollars and hours.
Conclusion
Vertex Software was founded on the idea of connecting groups and aligning 3D data in ways that have never been done before. And we’re doing it in a way that gives each department—from product engineering to manufacturing to sales and service—the ability to see information in their needed context. If you’re interested in seeing it in action, I encourage you to try it for yourself.
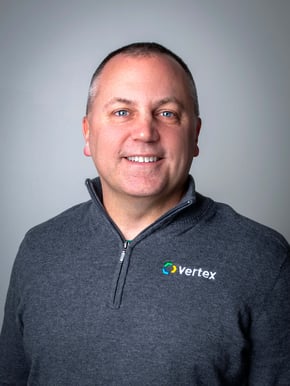
COMMENTS